Comprehensive Packaging Machine Repair Service for Quick and Effective Fixes
Recognizing the Key Components and Fixing Approaches for Product Packaging Device Maintenance
Efficient upkeep of product packaging machines pivots on a thorough understanding of their vital components, consisting of the frame, drive system, and sealing devices. Acknowledging common upkeep problems, combined with the execution of preventative strategies and troubleshooting methods, can substantially boost machine reliability.
Key Parts of Packaging Makers
Product packaging equipments are composed of several key components that work together to guarantee efficient and effective product packaging processes. At the core of these makers is the framework, which supplies architectural stability and houses the different operating parts. The drive system, typically a combination of gears and motors, facilitates the activity of parts, making it possible for specific procedure throughout the packaging cycle.
One more important component is the conveyor system, which transfers products via various stages of the packaging process. This is often enhanced by sensing units and controls that keep an eye on the position and speed of things, making sure synchronization and lessening errors. The filling system is crucial for precisely dispensing the ideal amount of product right into packages, whether in liquid, powder, or solid kind.
Securing devices, consisting of heat sealants or glue applicators, play a crucial duty in protecting plans, preventing contamination and prolonging shelf life. Additionally, classifying systems are essential for providing needed product information, making certain conformity with regulations. Ultimately, the control board, outfitted with easy to use interfaces, permits operators to handle equipment functions, display efficiency, and make changes as required, making certain optimal productivity and effectiveness in product packaging operations.
Typical Upkeep Concerns
Effective operation of product packaging machines depends greatly on normal maintenance to protect against usual problems that can interrupt production. Among these issues, mechanical damage is widespread, particularly in elements like motors, seals, and conveyors, which can result in unforeseen downtimes. In addition, misalignment of components can result in ineffective procedure, creating items to be inaccurately packaged or harmed throughout the procedure.
Another common maintenance problem includes the buildup of dirt and debris, which can conflict with the maker's sensing units and relocating components. packaging machine repair service. This not just impacts efficiency but can additionally pose safety risks. Moreover, lubrication failures can lead to enhanced rubbing, causing overheating and eventual part failure.
Electric problems, typically coming from loose links or worn-out electrical wiring, can interrupt machinery functions, leading to substantial production hold-ups. Lastly, software program glitches as a result of incorrect setups or out-of-date programs can hinder the machine's operation, demanding immediate intervention. Dealing with these usual maintenance issues proactively is crucial for making sure optimal efficiency and longevity of product packaging machinery.
Preventative Upkeep Techniques
Applying preventative maintenance approaches is vital for sustaining the effectiveness and integrity of product packaging equipments. These strategies incorporate a methodical strategy to upkeep, concentrating on the regular evaluation and maintenance of equipment to preempt prospective failings. By adhering to an arranged upkeep program, operators can determine damage on components before they bring about significant malfunctions.
Key aspects of a preventative upkeep approach include routine assessments, part, lubrication, and cleaning replacements based on maker referrals. Utilizing checklists can improve this procedure, making certain that no essential tasks are neglected. Furthermore, keeping precise records of maintenance tasks help in tracking the maker's efficiency with time, promoting educated decision-making concerning future maintenance needs.
Educating team on the significance of preventative maintenance boosts conformity and cultivates a society of positive care. Implementing a predictive upkeep part, using data analytics and sensing unit technology, can better maximize equipment efficiency by anticipating failures prior to they occur.
Repairing Techniques
When encountered with malfunctions or ineffectiveness in product packaging equipments, employing methodical troubleshooting techniques is essential for recognizing and solving problems promptly. The primary step in efficient troubleshooting is to establish a clear understanding of the machine's operational parameters and performance metrics. This involves evaluating the machine's specs, as well as any kind of mistake codes or informs presented.
Next, drivers need to perform a visual examination, examining for apparent indicators of damages, misalignment, or wear. This commonly consists of analyzing gears, sensing units, and belts to determine possible reasons of malfunction. Gathering operational information, such as production rates and downtime logs, can also supply understandings into repeating problems.
As soon as potential problems are determined, making use of a logical method to isolate the root reason is crucial. This may need testing individual parts or systems in a regulated manner. Participating in discussions with drivers who interact with the machinery on a regular basis can generate valuable pop over to this site feedback about unusual behaviors or patterns.

Repair Work and Replacement Ideal Practices
A thorough understanding of repair service and replacement ideal methods is important for maintaining the long life and performance of packaging equipments. Frequently analyzing the condition of machine parts permits prompt treatment, avoiding even more considerable issues that can bring about expensive downtimes.
When fixings are needed, it is vital to utilize OEM (Original Devices Manufacturer) parts to make certain compatibility and efficiency. This not only maintains the integrity of the maker but likewise upholds guarantee agreements. Furthermore, it is advisable to preserve a supply of crucial extra parts to help with read this fast substitutes and decrease operational interruptions.
For intricate repairs, engaging qualified technicians with specialized training in packaging machinery is advised. They possess the know-how to identify problems precisely and implement repair work effectively. Recording all fixing tasks and components replacements is essential for preserving a thorough upkeep history, which can aid in future troubleshooting.
Lastly, executing a proactive method, including regular assessments and anticipating upkeep methods, improves the integrity of packaging equipments. By adhering to these finest practices, businesses can ensure optimal device efficiency, visit their website minimize operational risks, and extend equipment life expectancy.
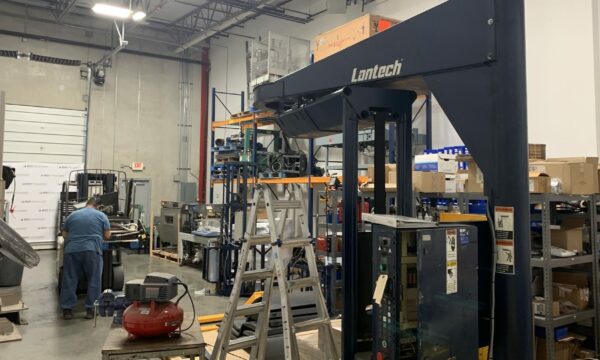
Final Thought
In final thought, an extensive understanding of packaging device elements and reliable upkeep strategies is important for ideal efficiency. By carrying out these techniques, organizations can ensure the durability and effectiveness of product packaging makers, inevitably adding to boosted functional productivity and reduced costs (packaging machine repair service).
Effective maintenance of packaging devices hinges on an extensive understanding of their crucial elements, consisting of the framework, drive system, and sealing systems.Efficient operation of packaging machines relies heavily on normal upkeep to protect against typical issues that can disrupt manufacturing.Applying preventative upkeep methods is vital for sustaining the effectiveness and integrity of product packaging makers. Furthermore, maintaining accurate documents of maintenance tasks aids in tracking the maker's performance over time, promoting educated decision-making relating to future maintenance needs.